Les dispositifs de transfert thermique
On distingue essentiellement les dispositifs externes, les internes et les autres possibilités. Nous présentons ici les différents dispositifs de transfert, et détaillerons le calcul des coefficients de film dans le paragraphe suivant.
2.1. Dispositifs externes
Il s'agit essentiellement des doubles enveloppes, continues ou formées de serpentins soudés, telles détaillées ci-après.
2.1.1. La double enveloppe simple
Elle est schématisée sur la figure 3.
La double enveloppe simple est généralement limitée à des volumes de 40 m3 sauf si elle est segmentée. Sa capacité de transfert est limitée surtout en réfrigération, et l’on y observe des risques de rétromélange du fluide de service et de dilution des gradients thermiques. Enfin, sa fabrication est coûteuse.
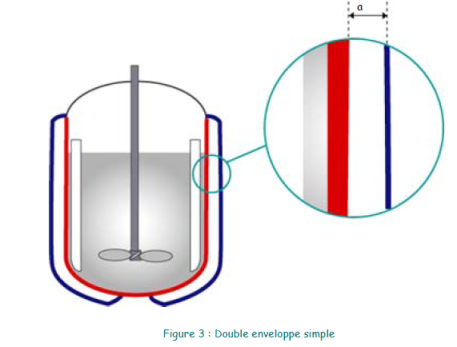
Le tableau 1 ci-dessous précise les surfaces de chauffe et les débits de fluide frigo- ou caloporteur en fonction des capacités des réacteurs à double enveloppe.
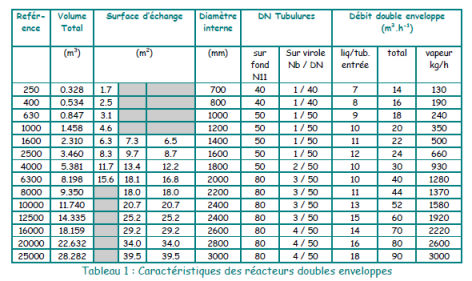
2.1.2. La double enveloppe a buses
Il s’agit d’une variante des réacteurs à double enveloppe.
Les buses sont utilisées pour améliorer le transfert dans les cas difficiles (cuves vitrifiées notamment). Elles provoquent une certaine turbulence locale et induisent un mouvement circulaire du fluide avec des vitesses tangentielles moyennes u typiques de l'ordre de 0.25 à 1.25 m.s-1, suffisantes pour que le régime d'écoulement soit turbulent. Dans ces conditions, les coefficients de transfert sont nettement plus importants que ceux relatifs aux enveloppes simples (deux à trois fois plus grands).
Les doubles enveloppes à buses sont limitées à des réacteurs de volumes de 40 m3. Leur capacité de transfert moyenne est améliorée par la vitesse d'écoulement du fluide de service au prix d'une perte de pression élevée. Le retromélange y est bien évidemment possible.
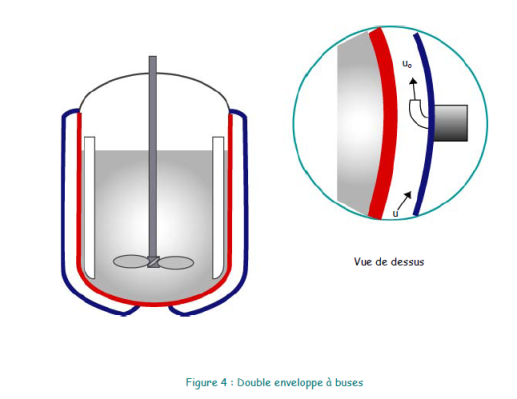
2.1.3. La double enveloppe spiralée
Une bande de métal enroulée en spirale est soudée à la paroi du réacteur. La double paroi, cintrée, est ensuite enfilée sur l'ensemble, fixée avec des cales d'épaisseur et soudée, comme le schématise la figure 4.
La double enveloppe spiralée est limitée à des volumes de 40 m3. Sa capacité de transfert moyenne est améliorée par la vitesse d'écoulement du fluide de service, et le rétromélange du fluide de service y est limité à la fuite d'ajustement e de la double enveloppe sur la spirale. Enfin, sa fabrication reste coûteuse.
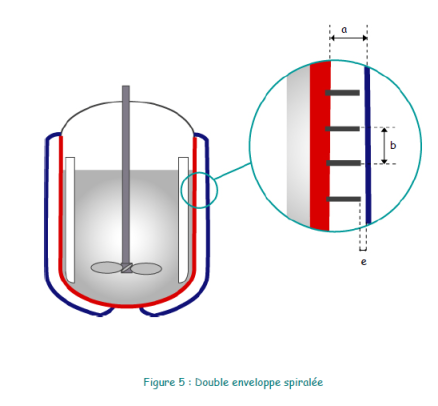
2.1.4. La double enveloppe a canaux rectangulaaires
Il s’agit d’un système analogue à la double enveloppe spiralée présentée ci-dessus, mais on s’assure de ne plus avoir de fuite entre chaque spire, si bien que e = 0, comme l’illustre la figure 6.
La double enveloppe à canaux rectangulaires peut être appliquée sur des réacteurs de n’importe quel volume. Sa capacité de transfert est moyenne à élevée, et le retromélange du fluide y est évité par la soudure continue des canaux. Toutefois, sa fabrication reste coûteuse et on lui préfère désormais les doubles enveloppes à demi-serpentins soudés.
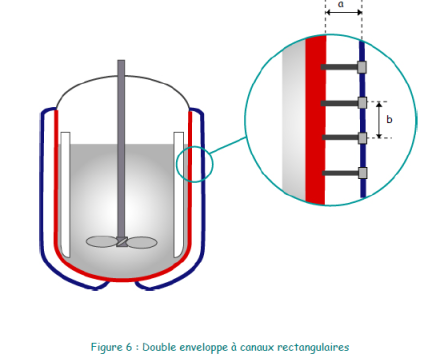
2.1.5. La double enveloppe a demi serpentins soudes
On utilise également la notion de demi-coques externes. Il s’agit d’un ou de plusieurs tubes, enroulés autours du réacteur. Les tubes peuvent être complets, mais sont la plupart du temps partiels (1/2, quelques fois 1/3 de tube) et sont soudés sur la paroi, comme l’illustre la figure 7. Ils sont parfois noyés dans un ciment conducteur qui améliore la répartition du flux thermique sur la totalité de la surface.
On utilise également des panneaux intégraux emboutis. Ces panneaux se calculent comme les serpentins, en utilisant la notion de diamètre hydraulique. Les coefficients de transfert sont sensiblement identiques à ceux obtenus sur une enveloppe spiralée pour des vitesses de circulation comparables.
Les demi-coques sont fréquemment disposées en plusieurs nappes, alimentées en parallèle, afin de limiter la perte de charge et de permettre un passage suffisant pour le liquide ou la vapeur. La surface de chauffe à prendre en compte dans le dimensionnement de telles installations est la surface mouillée, interne au réacteur. On considère en effet que la perte de surface externe entre les spires est compensée par l’étalement des lignes de flux thermique dans la paroi.
Le volume d’un réacteur maintenu en température par des doubles enveloppes à demi-serpentins soudés n’est pas limité. La capacité de transfert des dispositifs à demi serpentins est élevée, et il est possible d’utiliser des fluides sous haute pression. Par contre, leur fabrication est très coûteuse.
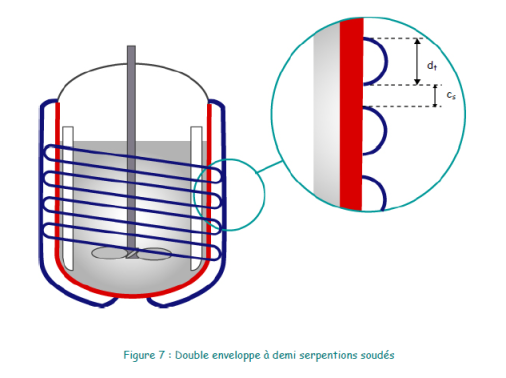
Le tableau ci-après, ainsi que la figure 8, permettent d’avoir une première approche des dimensions d’un appareil en acier inoxydable équipé de demi-serpentins soudés.
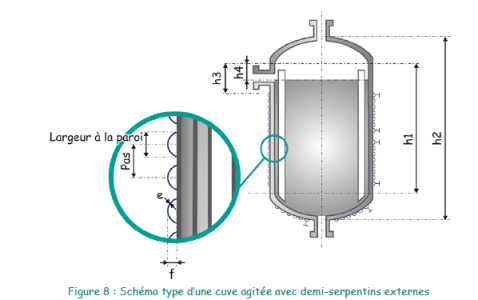
2.1.6. La double enveloppe a induction
Le chauffage est obtenu par des bobines d'induction (le plus souvent une en fond de cuve et deux latérales). Les courants de Foucaut générés dans la paroi du réacteur assurent le chauffage. Le refroidissement est obtenu par une double enveloppe, généralement en demi serpentin.
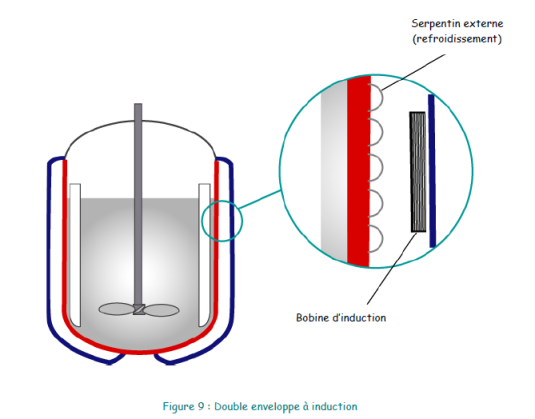
Les doubles enveloppes à induction permettent d’atteindre de fortes densités de flux (150 kW m-2). Elles se caractérisent par une absence d'inertie et de surchauffe, une absence de pollution, et une grande sécurité. Leur fonctionnement est possible entre -20 et 350 °C, et elles sont commodément adaptables aux réacteurs revêtus (vitrifiés…).
2.1.7. Conclusion
D'une manière générale, la double enveloppe coûte plus cher qu'un serpentin simple et son utilisation n'est à envisager que pour des raisons précises :
• La surface d'un éventuel serpentin est insuffisante. On le doublera alors par une double enveloppe,
• La présence d'internes obère trop la qualité de l'agitation,
• Le produit est encrassant et à tendance à se coller sur la paroi externe du serpentin (produits très visqueux notamment),
• Les problèmes de corrosion nécessitent l'utilisation d'un réacteur doublé en matériau noble, vitrifié, émaillé ou "caoutchouté".
Le choix entre la double enveloppe et la demi-coquille est à faire en fonction de nombreux critères. La double enveloppe, pour des conditions de fonctionnement normales, est d’un coût inférieur aux demi-coques. On privilégiera toutefois la demi-coquille, même à coût plus important, pour les raisons suivantes :
Coefficient de transfert plus élevé,
Possibilité d’utiliser des fluides à plus hautes pressions,
Minimisation du volume du fluide de chauffage dans le cas de l’utilisation de liquide, ce qui limite les temps de batch.
Enfin, on privilégiera l’utilisation d’une cuve à surface externe de transfert, pour des facilités de nettoyage, en batch notamment.
On sera amener à mettre des surfaces d’échanges internes quand il est impossible de mettre une circulation externe (produits très visqueux notamment), et que la surface externe est insuffisante.
2.2. Dispositif internes
Nous présentons ici 3 dispositifs internes de transfert thermique.
2.2.1. Le demi serpentin soude intérieurement
Il s'agit du même système que celui présenté figure 9, le serpentin étant soudé sur la face interne de la cuve.
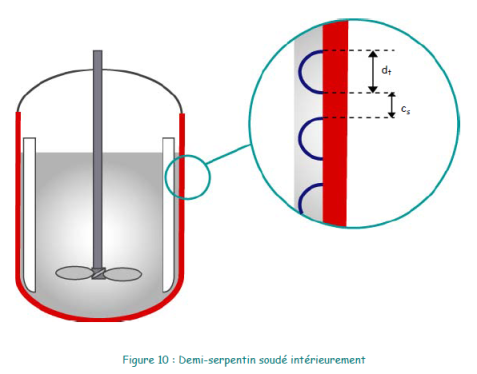
On retrouve les caractéristiques du demi serpentin externe : Le volume du réacteur n’est pas limité et la capacité de transfert est élevée (accroissement de la surface effective de transfert de 50 à 60% par rapport au demi serpentin externe). On observe aussi une diminution de la résistance de paroi (par amincissement de cette dernière, les demis serpentins étant moins épais que le réacteur). Enfin, ce type d’installation reste très onéreux.
2.2.2. Le serpentin helicoÏdal et les serpentins en épingle a la paroi
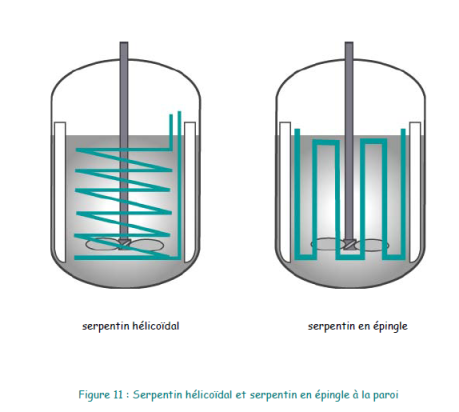
Ces technologies s’appliquent généralement à des réacteurs de volume inférieur à 40 m3, et pour des produits de viscosités limitées (environ 5 Pa.s). La capacité de transfert de ces deux technologies est élevée, et leur installation peu coûteuse. Toutefois, il est très difficile de les démonter ou de nettoyer le réacteur sans enlever le couvercle.
2.2.3. Échangeurs en chicanes
Ces géométries généralement réservées aux gros volumes sont schématisées sur la figure 12.
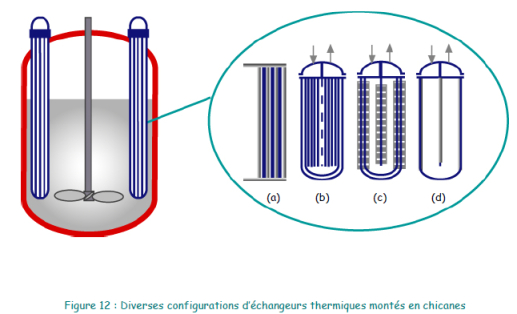
Ces installations possèdent des capacités de transfert élevées, mais sont limitées aux faibles viscosités (quelques mPa.s).
2.3. Échangeur extérieurs
Un échangeur extérieur monté en recyclage est parfois nécessaire dans les cas les plus sévères et pour les cuves de grand volume (figure 13). Le transfert ne dépend évidemment que de la qualité de l'échangeur extérieur choisi.
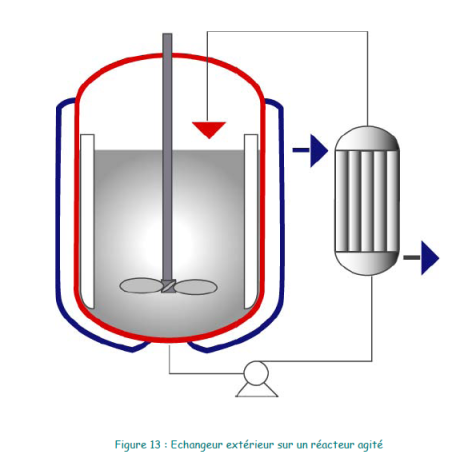
Un recyclage très important constitue en lui-même un dispositif de mélange et d'agitation. Le bien fondé d'une agitation par mobile tournant surajouté peut alors se poser. En présence de réaction chimique, lorsque le dégagement thermique est très important ou lors d'une marche globalement adiabatique, il peut être intéressant de pré refroidir l'alimentation.
Un autre moyen de refroidir est d’ajuster la pression de travail pour être à l’ébullition du solvant. Cette technique permet de traiter des charges thermiques relativement importantes.
Dans le cas d'évaporation importante d'un solvant avec retour par condensation (figure 14), il est également possible de sur refroidir les condensats recyclés. Cette technique est également utilisée dans le cas de réactions fortement exothermiques mises en oeuvre à température d’ébullition du solvant.
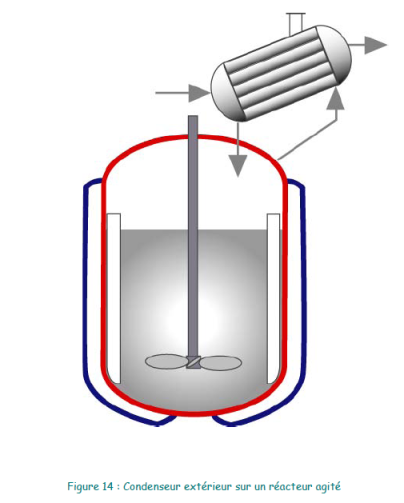
Cette technique s'applique quel que soit le volume du réacteur et permet des flux thermiques relativement importants.