Critères de sélections
Le dimensionnement d’un échangeur de chaleur nécessite la définition et le choix d’un certain nombre de caractéristiques de ses divers composants.
L’ingénieur procédé doit s’informer de l’implantation de l’appareil, de l’espace disponible et des éventuelles contraintes pour son installation et pour sa maintenance. Les limitations d’espace existent surtout quand l’échangeur doit être installé dans une structure ou bâtiment existant. Les restrictions sur l’espace disponible même sur une unité neuve peuvent affecter l’optimisation du coût de l’équipement. Mais c’est le coût de l’échangeur installé qu’il faut optimiser.
Les diverses caractéristiques d’un échangeur sont autant de variables qui seront définies par l’ingénieur procédé afin d’avoir le bon dimensionnement de l’équipement. Ces caractéristiques sont:
Le choix de la circulation des fluides,
Le type de boites de distribution et de retour,
Le diamètre intérieur des tubes et leur longueur et le pas de l’installation,
Le nombre de passes pour les tubes et pour la calandre,
Le nombre de calandres,
Les vitesses des fluides, et pertes de charge côté tubes et côté calandre,
5.1. Circulation des fluides
Dans certains cas, les impératifs de la fonction de l’appareil imposent un choix sur le côté du fluide (exemples : fluide à rebouillir côté calandre pour un kettle).
On mettra de préférence du côté tubes :
Le fluide sous la plus haute pression :
o Un tube résiste mieux à la pression intérieure qu’a la pression extérieure
o La plus grande épaisseur n’est pas à appliquer à la calandre dont la longueur est plus grande que celle des boites.
Le fluide à température élevée :
o Pertes thermiques limitées,
o Epaisseur de calandre minimale,
Le fluide corrosif,
Le fluide salissant
o Nettoyage mécanique des tubes plus facile que celui de la calandre,
- Le fluide de plus faible capacité calorifique globale (plus faible Cpm)
Par ailleurs, il faut prendre en compte d’éventuels impératifs de sécurité :
risques de ruptures,
risques de fuites (et dans quel sens selon les niveaux de pression).
5.2. Boites de distribution et de retour
On peut résumer les critères de sélection pour le choix de la technologie pour un échangeur tubes calandre par la représentation de la figure 7. Parmi tous les paramètres les deux principaux à prendre en compte sont l'encrassement et l'écart de température entre les deux fluides. Ce choix doit aussi être un compromis avec le coût de l’investissement. Il faudra s’assurer que la technologie tubes calandre est bien la meilleure pour le service demandé.
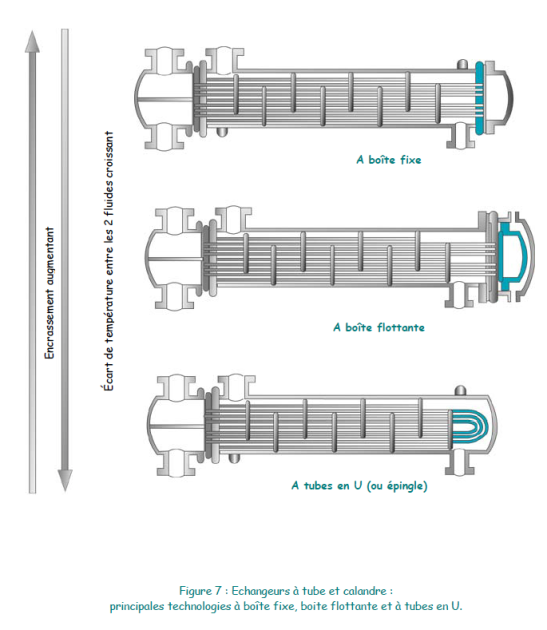
5.2.1. Dans le cas d'un fluide encrassant
Il faut alors:
de préférence le faire circuler dans les tubes, car il est alors possible de nettoyer l'intérieur sans avoir à démonter l'échangeur,
éviter les tubes en U, difficiles à nettoyer,
choisir un pas carré plutôt qu'un pas triangulaire si le fluide encrassant doit s'écouler dans la calandre.
5.2.2. Dans le cas de forts écarts de température entre les deux fluides
Pour des écarts de température supérieurs à 50°C, il risque d'y avoir des problèmes de dilatations différentielles, et il faut alors :
éviter d'avoir les deux plaques de distribution soudées à la calandre (et utiliser donc des boites P, S ou T, à tête flottante),
choisir éventuellement des tubes en U s'il n'y a pas de problèmes d'encrassement,
munir à défaut la calandre d'un soufflet de dilatation. Ce dernier assemblage est cependant fragile, et ne doit être employé que pour des pressions modérées (quelques bars)
5.3. Tubes
Le tableau 9 présente les caractéristiques d'appareils les plus fréquemment rencontrés.
De façon générale, il est plus économique d’utiliser des tubes de petit diamètre car l’appareil est alors plus compact (diamètre de la calandre plus faible) pour une surface et une longueur de tubes donnés. L’utilisation de petit diamètre est quelque fois impossible si on veut minimiser la perte de charge. Pour des applications avec des produits encrassant des diamètres plus importants sont utilisés surtout si un nettoyage mécanique est nécessaire.
Avec une même vitesse dans les tubes l’utilisation de petit diamètre augmente la perte de charge et le coefficient de transfert.
5.4. Nombre de passes
Le nombre de passes du côté tubes ou du côté calandre pour une spécification optimisée de l’appareil dépend :
des températures en opération,
de la perte de charge admissible,
de la vitesse des fluides,
de l’expérience.
Dans tous les cas le nombre de passes du côté tubes ou calandre influe sur la valeur de la différence de température logarithmique moyenne corrigée (F*ΔTLM). La dimension et le coût de l’appareil sont ainsi très étroitement liés à la sélection du nombre de passes.
5.4.1. Coté tubes
L’augmentation du nombre de passes côté tubes est utilisée pour augmenter la vitesse du fluide et donc le coefficient de transfert. L'ingénieur procédé doit toutefois limiter la vitesse en fonction de la perte de charge admissible.
5.4.2. Coté calandre
Le nombre de passes côté calandre où la configuration entrée – sortie (une passe, deux passes, split flow, flux divisé) est fonction aussi des températures en opération, de la perte de charge admissible, et de la vitesse des fluides.
5.5. Nombre de calandre
Le coût minimum sera pour un service donné d’avoir le plus petit nombre de calandre. En général on a une seule calandre si on n'a pas de croisement.
Dans le cas où l'on croise les températures (température du fluide chaud en sortie inférieure à la température du fluide froid en sortie), un montage avec plusieurs calandres en série peut être nécessaire et être la meilleure solution. Ce cas peut se présenter dans des récupérations de chaleur entre fluide de procédé. Ce cas correspond à un échangeur à une seule calandre avec une longueur de tubes égale à la somme des longueurs de chaque calandre.
5.6. Vitesse des fluides, perte de charge
Normalement l’optimum dans le dimensionnement d’un échangeur est quand toute la perte de charge disponible est utilisée. Dans ce cas, on a le coefficient d’échange maximum et le minimum de surface d’échange.
En effet l’échangeur est installé dans un circuit pour le côté tubes et dans un autre circuit pour le côté calandre. Un dimensionnement préliminaire de pompes par exemple donne la valeur de la perte de charge considérée. Pour un condenseur de colonne travaillant sous vide on définit la pression en tête de la colonne et celle à l’aspiration de la pompe à vide. Dans ce cas la perte de charge maximum dans le condenseur est déterminée.
La perte de charge peut être minimisée par le choix du type de calandre. Pour une même longueur et diamètre de calandre, la perte de charge dans une calandre type E (une passe) peut être divisée par huit en utilisant une calandre type J (à écoulement divisé).
Le débit est divisé par deux donc la perte de charge par quatre,
La longueur de passage dans l’appareil pour le flux est divisée par deux donc la perte de charge par deux,
Donc la perte de charge totale est divisée par huit.
Pour des échangeurs importants, une analyse de la valeur devra être faite entre l’investissement initial et la puissance électrique consommée avec une perte de charge variable.
Toutefois la vitesse des fluides doit être limitée afin d’éviter des dégâts sur l’appareil par les vibrations induites ou par de l’érosion.